The inventory system in your eMaint X5 account will allow you to track the parts needed to keep your equipment running.
This session will show how to create part records and how to configure the Inventory module correctly. You will also learn how to associate suppliers with parts and how to make On-Hand Adjustments.
1 - Creating Part Records
Creating a new part record is a process similar to creating any other records in the system. In order to add a new part you need to:
- Start by clicking on the “New” button in the upper right corner
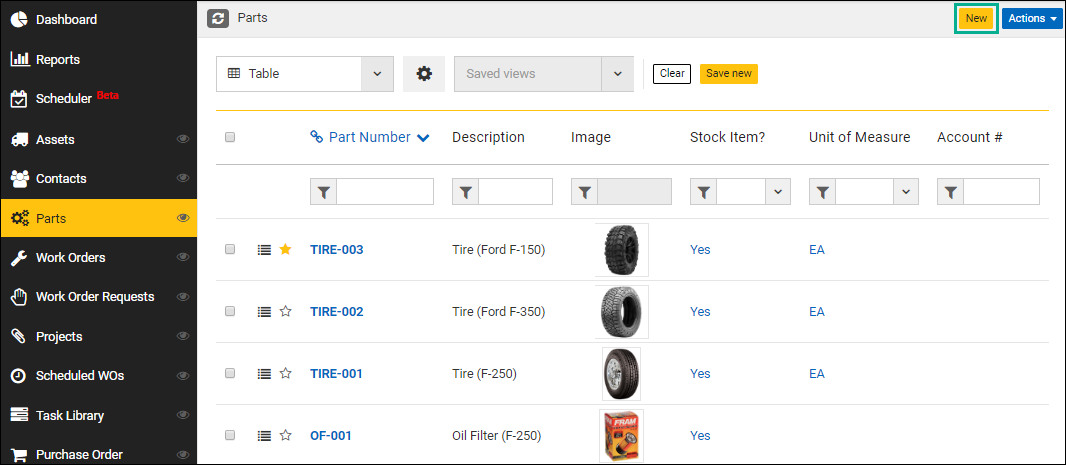
- A - Specify the “Part Number” (maximum length of 15 characters).
- B - Fill in the “Description” field.
- C - Stock Item? Yes or No (choose one) This is for items that you need to have in your stockroom at all times. This field dictates whether the part is automatically pushed into the reorder list the on-hand value equals or falls below the reorder point.
- D - Click on “Save” to complete the record.
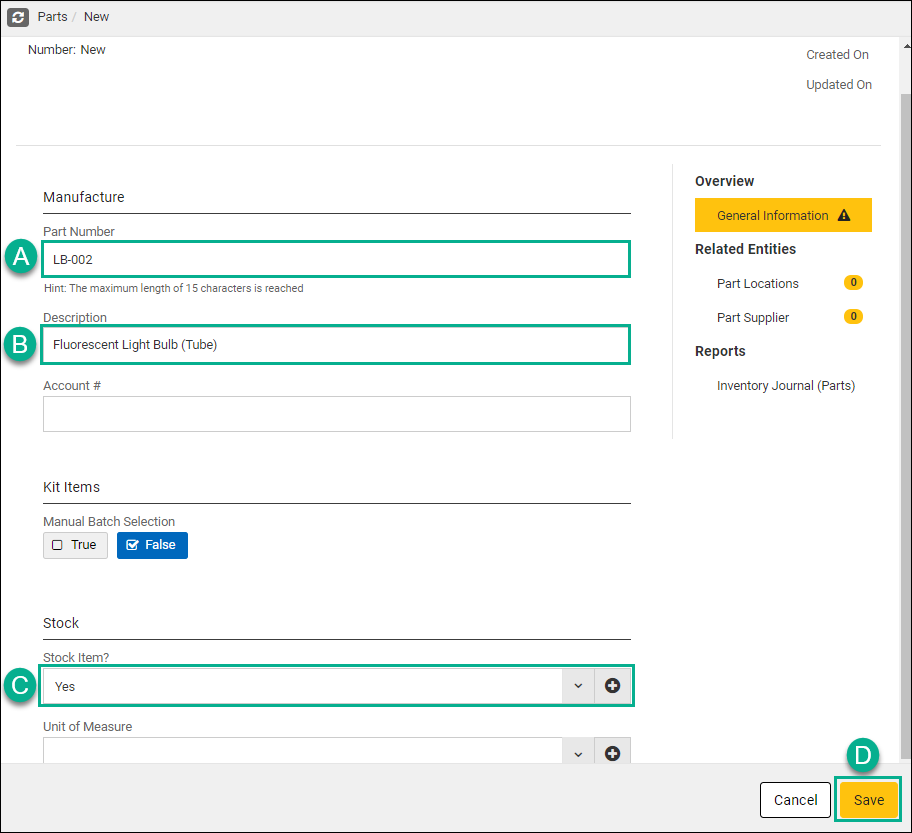
- If you wish to add an image to a part, click on the image icon next to the part number, then select an image from your computer.
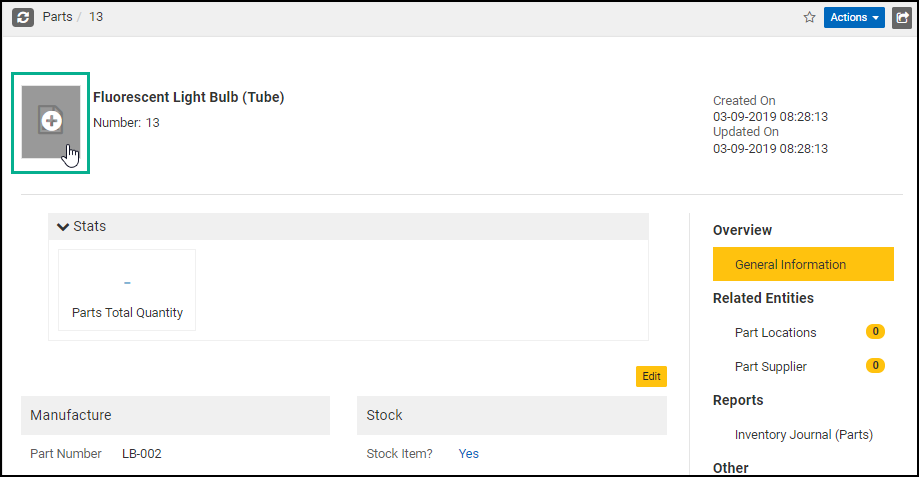
2 - Part Locations (Setting up Reorder Point, Reorder Qty and On-Hand)
- A - Next, go the Related Entities section on the right side of the record and select “Parts Locations” entity.
- B - Enter a value into the “Reorder Point” (amount that will trigger reordering).
- C - Enter a value into “Reorder Quantity” (default amount to be reordered);
- D and E - Choose a “Location”, then click on the “Add” button.
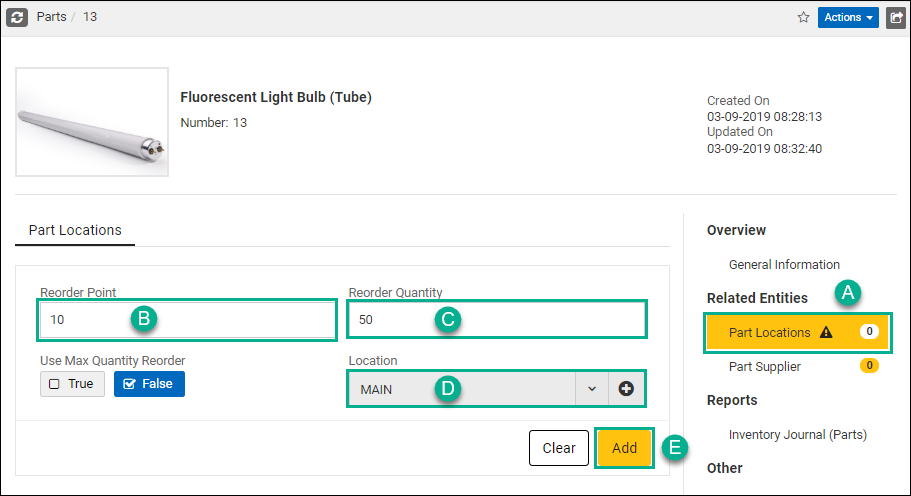
- F - The last step is to click on “Save” at the lower right of the screen.
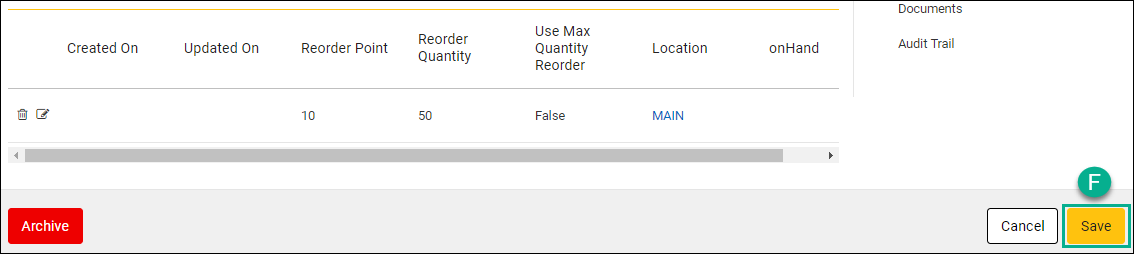
Note - In the near future, the “Use Max Quantity Reorder” button will be tied to the Requisitioning system. If you say true, then when the system auto creates a Requisition for re-ordering, it will generate a requisition only for the difference from what you have on hand and your reorder quantity. (Example: If you have 10 on hand and your reorder qty is 100, the system will generate a Requisition for 90 parts.
When you first create a Part record, the on-hand amount is “Zero” by default. To add an On-Hand amount, you will need to make an adjustment. To do so, you will need to:
- A - If not already in the “Part Locations” related entity, go back into this area.
- B - On your saved Location entry at the bottom, click on the Adjust icon [three lines with sliders] on the far left of the record entry.
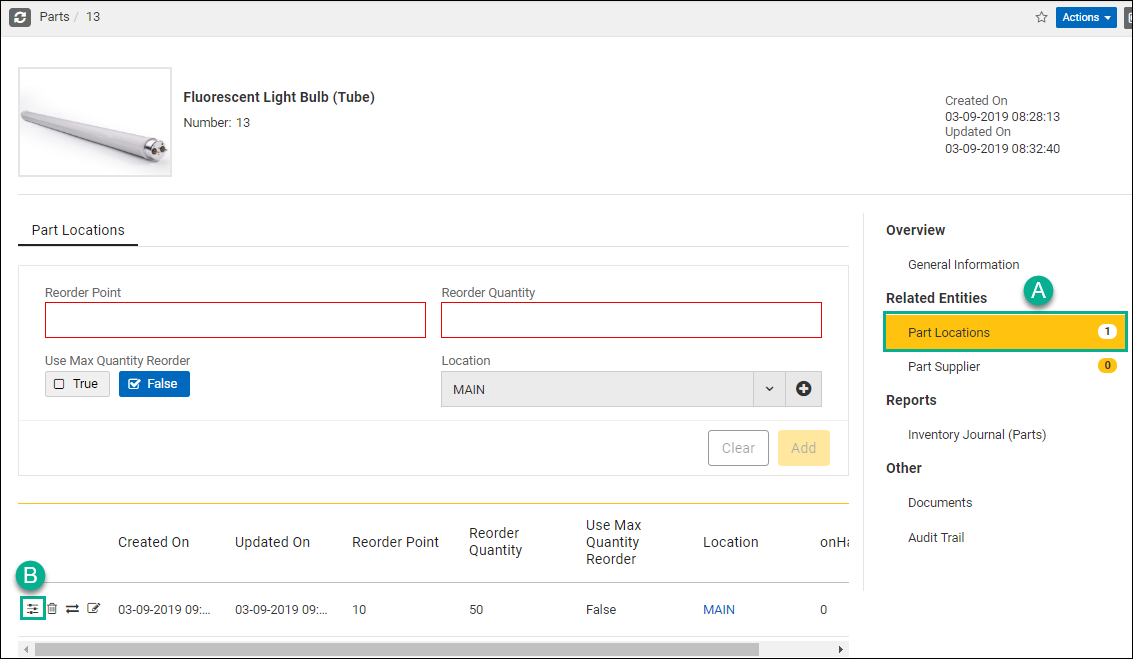
- C - Here you will enter the onhand quantity either by using the + or - buttons or by directly entering a number into the “adjust amount by” field and clicking OK [positive amounts do not require a + sign; however, negative amounts do require a - sign].
- D - Select the “Adjustment Type”, such as Physical Count.
- E - Enter the “Unit cost for the new part”.
- F - The last step is to click on the “Adjust” button.
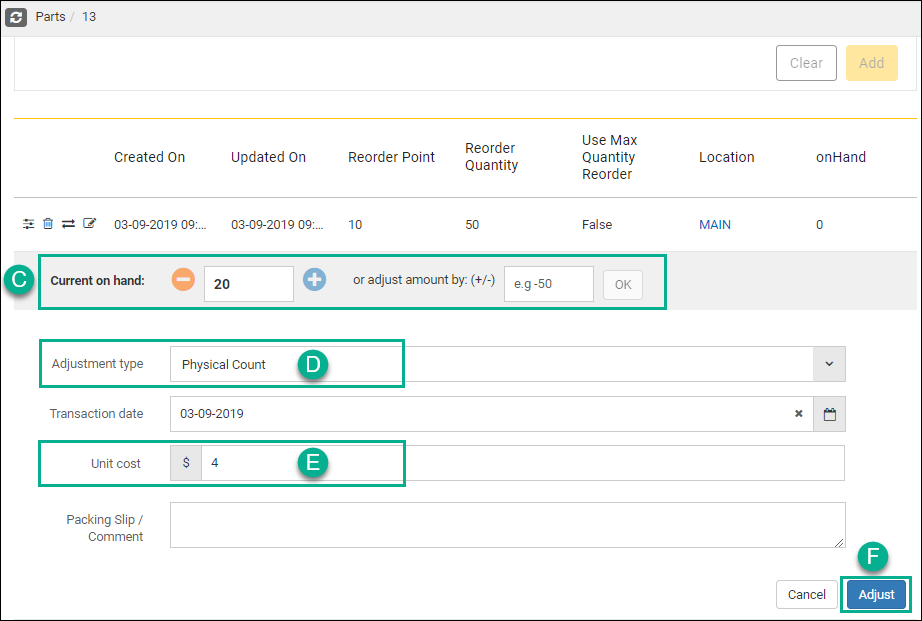
3 - Associating Suppliers with Parts
For each part that you have in inventory, you may have one or multiple suppliers. You may add as many as you would like and specify one as the “Default”.
In order to be able to associate suppliers with parts, you first need to make sure that they have been entered into your “Suppliers” list. Assuming your suppliers are already in the system, follow the steps below:
- A - Go into the “Part Supplier” related entity.
- B - Select a “Supplier” from the list. Change currency if needed.
- C - Enter a “Unit Cost” for the part.
- D - Click on the “Add” button.
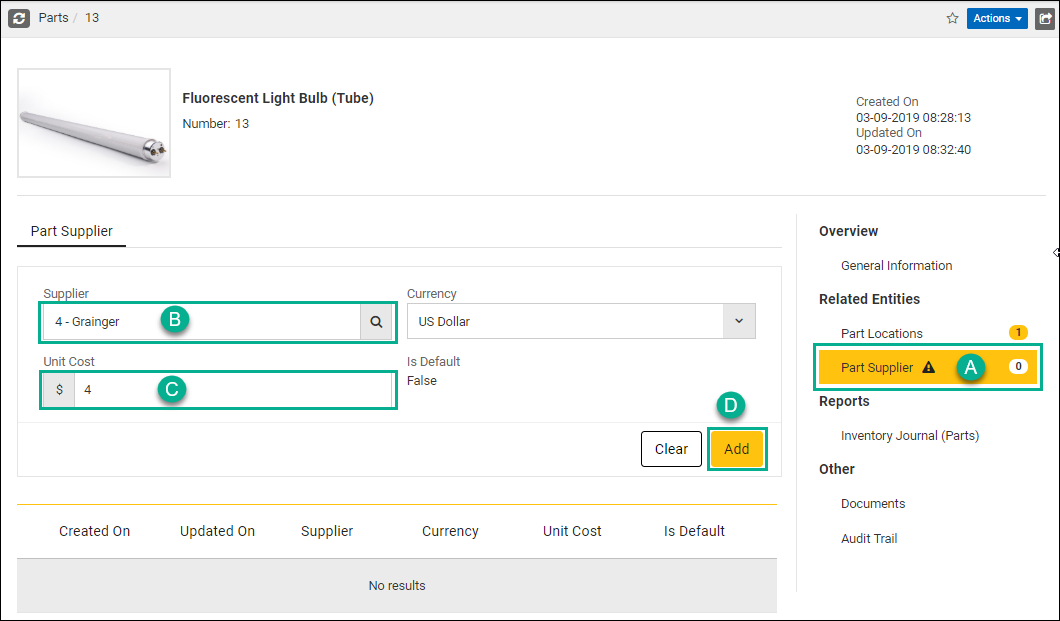
Note - You can repeat this process if you need to associate more Suppliers with this item.
- E - Click the “Save” button.
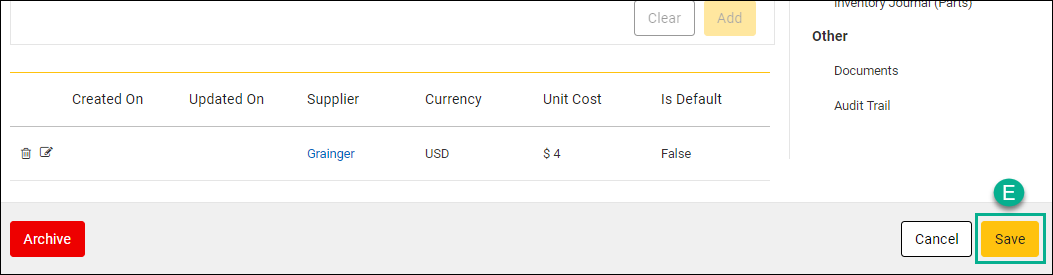
As mentioned before, you may have multiple Suppliers for each Part. However, you should have one Supplier indicated as your “Default”.
- A - Click on the check box icon at the far left of the record.
- B - Answer the question, “Set as the default supplier?”; if yes, then click on the “Ok” button on the right.

4 - Making Part Adjustments
To make a part adjustment you will need to navigate back to the “Part Locations” related entity, then:
- A - Go to the Location entry and click on the Adjust icon [three lines with sliders] on the far left of the record entry.
- B - On your saved Location entry at the bottom, click on the Adjust icon [three lines with sliders] on the far left of the record entry.
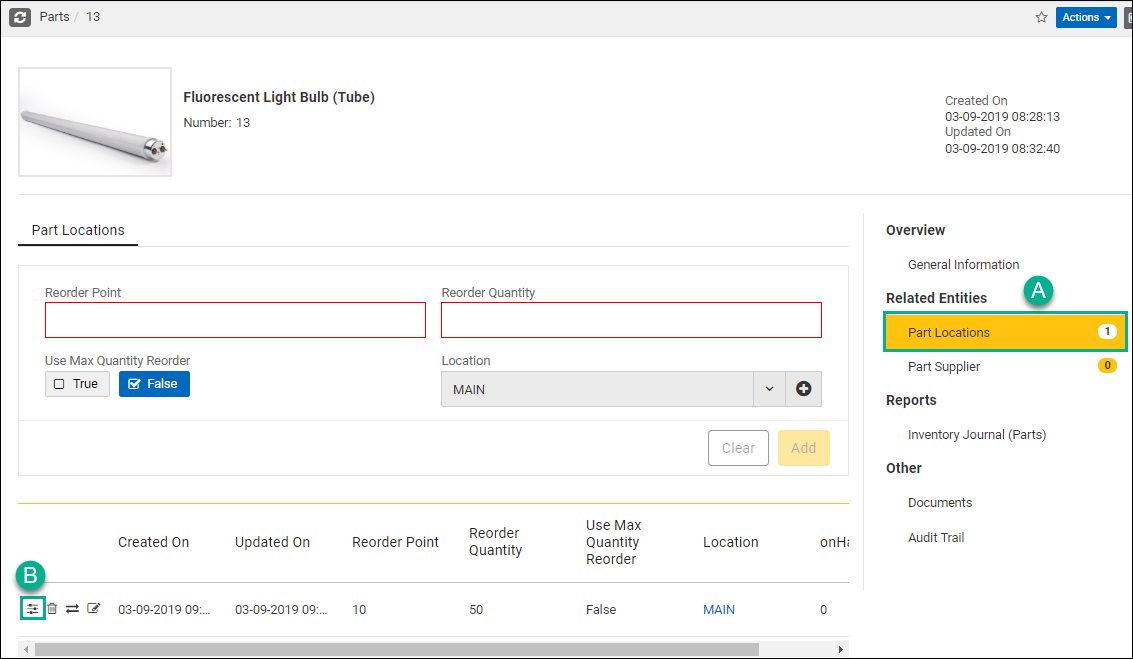
- C - Here you will enter the onhand quantity either by using the + or - buttons or by directly entering a number into the “adjust amount by” field and clicking OK [positive amounts do not require a + sign; however, negative amounts do require a - sign].
- D - Select the “Adjustment Type”, such as Physical Count.
- E - Enter the “Unit cost for the new part”.
- F - The last step is to click on the “Adjust” button.
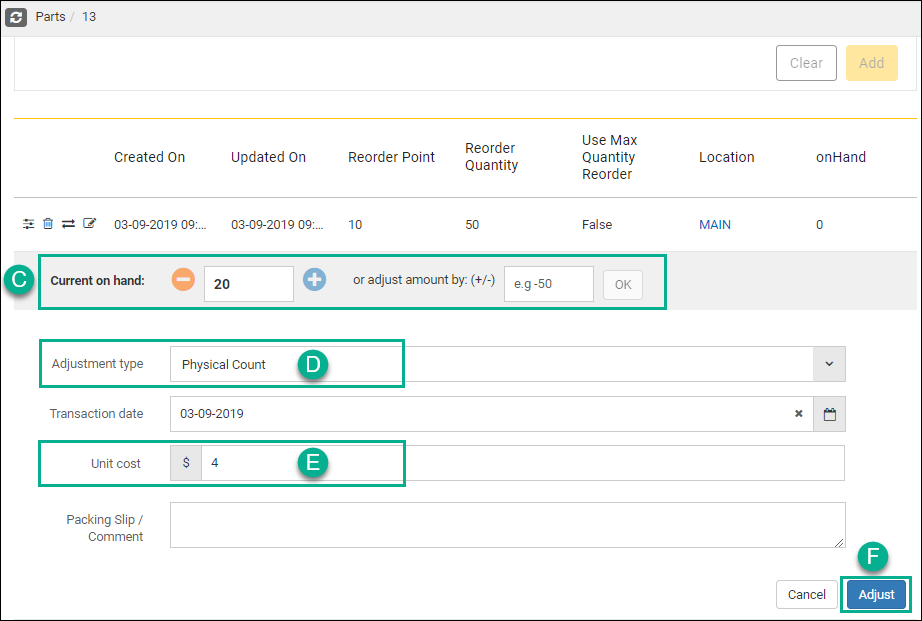
Note - For negative adjustments, you won’t need to provide an Unit Cost.
5 - Viewing Inventory History
You will be able to display all of the transaction history for each part in your inventory. To do so:
- Go to the related information on the right side of the screen. Locate the “Reports” heading and select “Inventory Journal (Parts)”.
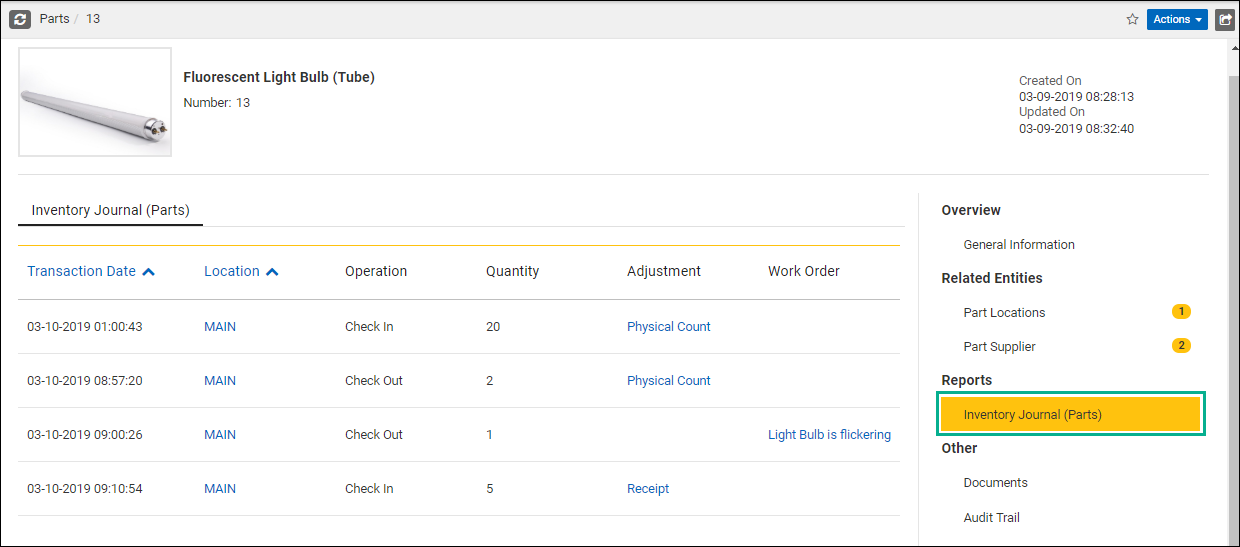
The history will show all the part’s Check ins (Positive Adjustments and PO Receipts) as well as Check outs (Negative adjustments and Issues to WOs).
6 - Audit Trail
Associated with each part in your inventory, you will have a complete history of any changes ever made to a part item. To access this area, click on “Audit Trail” on the right side of the screen.
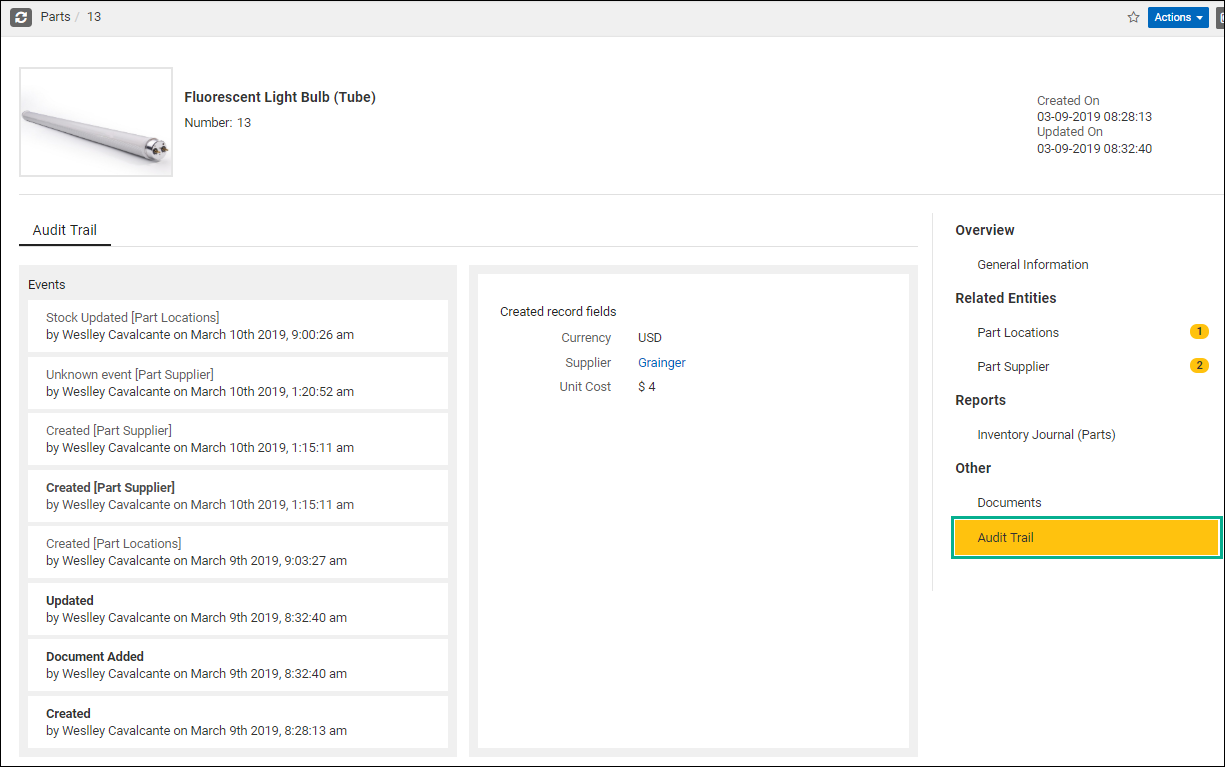
The “Audit Trail” information will be displayed on the left side of the screen, where you will see all of the “Events” that have happened within that record and its related entities. These events will be displayed in chronological order (date/time) starting with the date the part was created.

7 - Barcode Labels
You can view and and print Barcode labels for the parts in your inventory from the Parts list view in your system. To do so:
- Click the Actions icon (the three horizontal lines) next to a record.
- Select the “Get Barcode” option in the menu. The barcode will be generated as a PDF file and download to your computer.
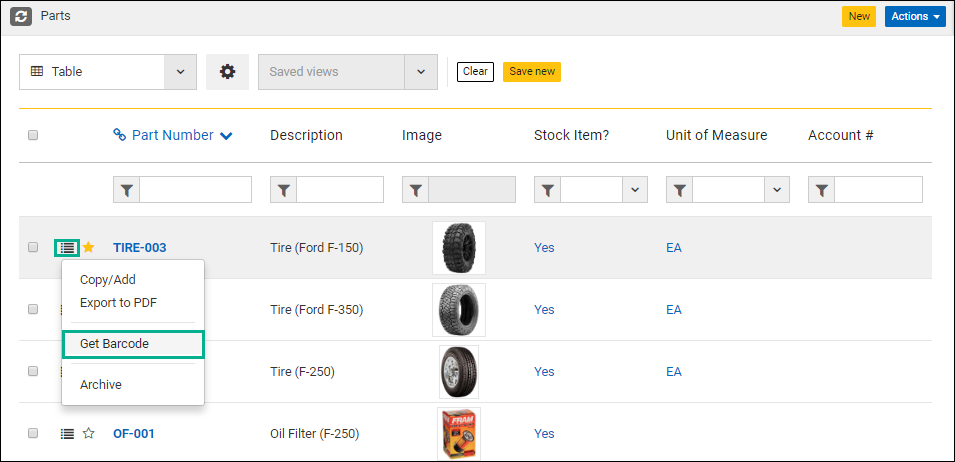
Select the file and a popup window will then display that item’s label.
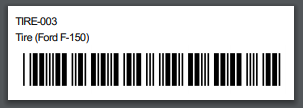